Electrical work must be carried out in compliance with fire safety standards. A corrugated metal pipe is more often used as one of the protective means when installing a two-, three-core cable. It performs a fire function and protects the cable from mechanical stress.
Metal wire for electrical wiring
Corrugated metal pipe is a special protective channel for wiring, hollow inside. More often produce tubes of galvanized steel, which ensures their moisture-proof properties.
Corrugated pipes are used in the following cases:
- Laying the electric cable behind flammable panels or on top of them: frame, wooden panels, lining, polymer finishing materials.
- Laying a metal corrugated hose for electrical wiring in a cement floor screed or other concrete structures. In addition to mechanical cable protection against squeezing, the pipe allows you to change old wires to new ones if necessary without dismantling the monolithic fill.
- Outdoor wiring device from the street: powerful cables for lighting, sophisticated equipment, etc.
- Installation of underground power supply systems.
- The wiring device is close to gas pipelines, heating communications.
- Parallel cable routing to prevent it from crossing.
According to the PUE (clause 2.1.64), the metal corrugation for wiring must be completely tight.
Types of corrugated metal pipes
On the market you can find the following types of tubes:
- Stainless steel. They have the highest cost among the options presented.
- Galvanized. They have a special fabric, which ensures the integrity of the connection of the corrugation links.
- Steel with polymer (PVC) braid. Designed for cable installation in places of increased explosion hazard, in soil, water. This type of pipe is characterized by increased tightness.
- Tin. The lightest kind of metal corrugation. It is relevant when wiring in places with high humidity. The tightness of the joints of the link is ensured by a special polypropylene film.
Protective channels are always cut in one piece per meter of cable. Joining of two cuts of a tube is not allowed.
How does metallofra work
Corrugated metal hose works on the principle of a containment barrier at high pressure on the sleeve with the wiring. This is especially true for cable in the soil. The stiffeners here are the links of the tube.
If we take for comparison smooth-walled and corrugated pipes with the same conditional diameter, the area of the second will be significantly larger than the first. Here you can track the principle of the protective channel according to the formula from the school course of general physics:
- P = F / S,
where the values are interpreted as follows:
- P is the pressure on the pipe;
- F is the force that acts on the surface perpendicular to its plane;
- S is the area of the desired surface.
After analyzing the formula, it becomes clear: the larger the total surface area that is subjected to mechanical stress (external pressure), the smaller it is for every cm2 of sleeve.
Technical characteristics of corrugated metal hoses
All metal corrugations for electrical wiring have a number of their technical parameters and characteristics.They should be considered when choosing channels. More often information is presented in the form of marking on pipes. Corrugated tubes made of metal have the following parameters:
- Withstand load - up to 125 N / cm2, up to 320 N / cm2, up to 750 N / cm2, up to 1250 N / cm2, up to 400 N / cm2: very light, light, medium, high, very high load, respectively.
- Impact strength - from 0.5 kg / 100 mm to 6.8 kg / 100 mm.
- Rigidity - solid, flexible, especially flexible, memory tube. Moreover, the bending radius can vary within 25≤R≤150 mm.
- Temperature operating conditions - from -45 to +400 degrees Celsius.
- The roughness coefficient is 0.008.
- Thermal conductivity - 17 W / m * K.
- Internal section - 16-50 mm.
Corrugated metal sleeves serve more than 30 years.
How to choose a metal corrugation
The protective channel for laying the cable is selected according to various criteria, according to the conditions of the electrical installation.
The first condition of choice is the inner section of the sleeve. Here, they rely on the electricians section, which is mounted:
- eyeliner to lighting points - 16 mm;
- to switches or sockets - 20 mm;
- installation of a low-current cable (antenna, telephone, Internet) - 25 mm;
- from the shield to the junction box - 25 mm;
- connection of two shields to each other - 32 mm;
- cable transition between floors - 40 mm;
- laying of wires in the ground, collector pipes - 50 mm.
According to the level of flexibility, a corrugated pipe is selected taking into account the maximum possible pressure on the mounted channel:
- Light pipe has a low level of strength. Designed for wiring under suspended or suspended ceilings, for plasterboard structures, for lining. Such thin-walled corrugated metal pipes for electrical wiring have the lowest cost.
- Heavy tube of medium strength. It is allowed to be laid in a cement screed, plaster, soil.
- Extra heavy sleeve. It is indicated for use in rooms with high fire safety requirements: public institutions with high attendance, hospitals, schools, kindergartens.
Experts recommend paying attention to the channel manufacturer. The most popular are:
- IEK (Russia);
- Legrand (France);
- Frankische (Germany).
When buying, it is advisable to ask the seller for a quality certificate for the selected product.
Advantages and disadvantages
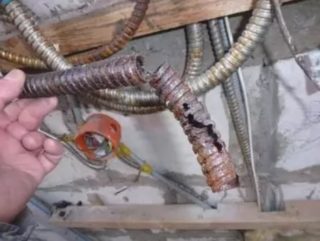
All corrugated metal pipes for wiring have several advantages:
- high service life (30-50 years);
- protection of the laid cable from small pests, rodents, mechanical damage;
- simplicity of installation of the channel on wires;
- the ability to replace the old wiring with a new one without complicated dismantling;
- subject to grounding, reliable protection against electric shock;
- resistance to moisture, pressure, temperature differences;
- zero flammability;
- relatively light weight.
The disadvantages of using a protective corrugated channel include:
- high costs for wiring;
- the complexity of the process;
- risk of accumulation of condensate in the channel and, as a result, a decrease in wire resistance.
Metal corrugations are sold in coils or meters.
Materials and brands
For the production of protective channels, stainless or galvanized steel is often used. The first option is more durable (MPN brand). Stainless steel pipes are characterized by increased rigidity and tightness.
Another brand of products is MGPng. Such a steel corrugated pipe is produced using a special method of winding the links, using a sealing thread and thickened insulation. The sturdy tube is characterized by increased flexibility.
MRPING brand - products with a top polymer coating-braid.
If you need reliable protection of the cable from water, oil products, it is better to give preference to the latter option.
Wiring in a metal corrugation
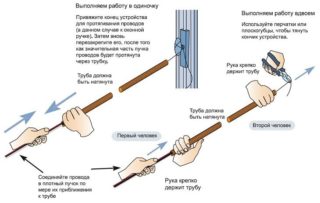
To freely skip the desired cable length along the sleeve of the corrugation, you need to prepare:
- a piece of metal pipe equal to the footage of the cable;
- piece of electrical wire;
- a cap from a ballpoint pen or felt-tip pen;
- a piece of sandpaper.
The work is performed as follows:
- Using the skin, the protruding faces of the cap are removed so that it takes a smooth cylindrical shape.
- Put the item on the end of the cable. Run it into the corrugation and gradually push it until the cap appears on the other side of the channel.
- It is advisable to perform the entire operation on the weight of the iron pipe in order to facilitate the passage of the wire through the channel.
This method is suitable for using a tube in which an old cable was previously laid. In the new channel, the device wires are performed as follows:
- One end of the conductor (a special wire in the cavity of the pipe) is slightly released.
- They pierce a two- or three-core cable 1 cm from its beginning so as not to damage the cores. Pass the end of the wire through the wire and twist it with a loop. The remains of the conductor can be insulated so that they do not cling to stiffeners in the protective sleeve when passing the power cord.
- The second (opposite) tip of the cable wire must be tied to the “anchor” (radiator, strong metal rail).
- It remains to pull the metal fiber onto the wire with both hands until its opposite end appears on the other side of the tube.
The mounted sleeve with cable is attached to the wall of the house in special clip-on clips. They are placed in increments of 30-40 cm.