Material for insulation of facades is laid according to a certain technology. Plates must be firmly attached to the bearing surface. It is not enough to limit yourself to the use of special plastic dowels. Full installation can be called if glue for mineral wool was applied to each sheet. Compliance with this rule is fundamental for the long and efficient operation of the heat-saving layer.
What is glue intended for?
Mineral wool slabs designed specifically for vertical walls have a higher density and fit well to the base. But due to the irregularities of the latter, channels are formed between him and the heater anyway, through which air passes freely. This reduces the heat-insulating ability of the cake. Adhesive for mineral plates based on basalt helps to solve the following problems:
- It is a reliable clamp of insulation, not allowing it to move under its own weight in conditions of natural shrinkage, temperature changes in the walls of the building.
- It blocks the channels for the movement of cold masses under a layer of stone wool.
A high-quality product must itself have heat-insulating properties so as not to become a cold bridge for passing the dew point into the body of the supporting structure.
Varieties of fixing compositions for mineral wool
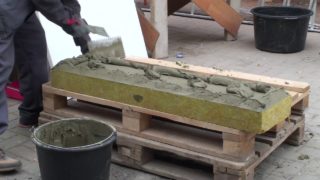
You can classify all known ligaments for fixing insulation mats according to the following criteria:
- Internal composition - this parameter determines the ability of the material to create adhesion to the structure of basalt wool and to the base of the wall.
- Mechanical strength - the stronger the hardened fixing mass, the larger the sheets can hold by weight.
- Temperature application - there are mixtures that can be effectively operated in harsh winters with very low thermometer bars.
- Hardening speed - a parameter that affects the ease of installation.
- Execution - there are dry formulations either in the form of foam.
For the most part, the manufacturer seeks to create universal adhesives for mineral wool on the walls, which are convenient to use in any conditions.
Dry mix
Bulk product to bring into working condition requires a connection with water. It has a complex composition based on cement and various binders. A fiber of inorganic origin is present in the structure as a reinforcing component. A dry bundle is not a combustible material and can be used in the insulation of buildings of any fire hazard category.
The solution has a certain period of hardening and allows the builder to timely align the insulation boards, ensuring the comfort of work.
Polyurethane foam
Polyurethane-based mineral wool glue goes on sale in cylinders for an assembly gun. The action of compressed air stream of foam through the tube goes directly to the sheets of stone wool. The structure of polyurethane allows it to increase its volume when in contact with the atmosphere, so several liters of working mass can fit in a small-looking cylinder.
Mounting adhesive foams for mineral wool are very convenient to use and significantly speed up the process of warming building facades.
Positive and negative properties of binders
The strengths of the adhesive for mineral wool insulation on a dry basis include:
- good adhesion to the surface;
- mechanical strength of the hardened material;
- the structure is resistant to moisture absorption and has a large number of cycles of exposure to low temperatures;
- absolute vapor permeability;
- ease of use and relative cheapness of the product.
Dry glue for stone wool meets environmental safety standards for direct use in residential construction.
Among the shortcomings can be noted the seasonal limitations of the application in work, the need for additional cooking, the original product itself has a large volume and mass, which increases the cost of its transportation.
Polyurethane polyurethane foam has the following advantages:
- excellent adhesion with any known building materials;
- the structure does not transmit heat;
- it is possible to carry out work in frosty conditions, in wet weather;
- already prepared for the intended use;
- lightweight convenient cylinders reduce the time for applying a layer on the working plane;
- the frozen mass does not absorb water.
The disadvantages of the adhesive for basalt insulation include the fact that polyurethane foam is a combustible substance, it is less durable than the dry fraction, has a high cost.
Parameters of technical and operational properties
In order to choose glue for glass wool for the specific task of insulation, it is important to know its characteristics. Usually they are indicated by the manufacturer on the packaging and can be easily found. Technical give an idea of the binder, the density of the structure, the flow rate of the liquid in the preparation of the working solution, the consumption of glue per square surface. The operational ones show how the adhesive base behaves, what loads it can withstand, in what environmental conditions it works normally.
Glue coating technology
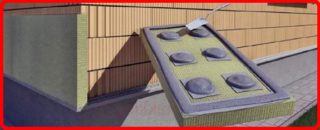
To carry out installation of insulation on the facade of the building, you will need such tools and materials:
- builder trowel (trowel);
- notched trowel;
- long grout;
- electric drill with mixer;
- dry glue for a miniplate, for example, Ceresit CT180;
- plastic dowels (fungi).
The very first stage before applying the adhesive mass to the insulation sheet is the removal of dust, dirt particles, grease stains from the wall plane. The base must be smoothed as much as possible, putty cracks, remove peeling plaster.
After preparation, the main operations are carried out:
- Around the perimeter of the building in a strictly horizontal direction establish a socle profile.
- A deep penetration primer is applied to the wall.
- A working solution is prepared - water is added to the bulk mixture at the rate of 200 ml per 1 kilogram of glue and mixed with a mixer.
- According to the technology, the solution is left for 3 minutes, and then mixed again.
- Reinforce the working surface of the basalt mat by rubbing it over the entire plane of the glue through a mesh with a spatula.
- Using a trowel around the perimeter of the insulation sheet, the mass is applied in strips from the edge of a width of five centimeters.
- At three points in the center along the length, cakes of the adhesive solution are applied.
- The plate is supported on the profile, applied to the wall and pressed with a long grout.
- The protruding layer of the retainer is removed from the surface.
It takes about three days to completely harden the mortar and to fix the mats well; therefore, each plate is immediately fixed with plate-shaped dowels per one square meter - 6 pieces.The following layer of sheets is staggered to ensure structural integrity.
Mineral slabs should fit tightly with the formation of seams of no more than two millimeters.
Glue costs
The consumption of working material mixed with water largely depends on the type of base, the quality of the basalt mats, the working technique of a particular construction team and the brand of glue. Manufacturers of dry running mixes claim that on average costs per square meter of surface are from 4 to 9 kilograms.
In the hot period of time, when the solution dries quickly, there will be more waste, consumption will increase.
A brief overview of modern adhesives
Ek thermex - adhesives for heat-insulating plates, which are effectively used for interior work and outside of facades. They are suitable for working with mineral materials and well fix polystyrene sheets and reinforcing mesh on vertical and horizontal surfaces. The mixtures are plastic and create good adhesion with the bases of brick, concrete and plastered cement-sand mortar.
Ceresit CT180 - facade glue for insulation based on cement, mineral fillers and polymer-type modifiers. The mixture in operation has a small flow rate of five kilograms per square meter of surface. Frost resistance Ceresit CT180 is in the aisles of 100 cycles, which makes the product a high class. The hardened mass retains its design indicators in the temperature range from +70 to -50 degrees Celsius.
Ceresit CT190 - a mixture of this brand is produced in two versions - winter version and summer. The compositions can only be operated in conditions of positive temperatures with modes 0 - + 15 and + 5 - + 30 degrees Celsius, respectively. The winter mixture after curing for eight hours may be subject to a temperature drop of -5 degrees Celsius.