Warming the house with mineral wool under the plaster is an effective technology that is available even to a novice master. Carrying out this event will significantly reduce heating costs, create a comfortable microclimate in the room with an optimal level of humidity and temperature.
Why mineral wool
Mineral wool for the facade for plastering is made in the form of slabs measuring 50 × 100 cm and 60 × 120 cm, with a thickness of 50 mm, 100 mm and 150 mm. The most popular material among builders is Knauf and Rockwool products with a thickness of 100 mm.
The choice of mineral wool for wall insulation on the outside for plastering is due to the following advantages of the insulator:
- Low thermal conductivity providing excellent protection against heat and frost.
- Low density. It provides low weight, so that excessive pressure is not created on the supporting structures.
- Excellent soundproofing. Street noises do not enter the room.
- Fire resistance. The heater does not burn, in case of fire it will become a barrier to the flame.
- Vapor permeability. Stoves pass gases well, provide effective removal of moisture from the building. Minvata for plaster can be installed on walls made of wood, brick, aerated concrete and other materials with ventilation properties.
- Biological inertness. The fungus and mold do not start in the material; animals and insects avoid it.
- Ecological cleanliness. Thermal insulation does not emit substances harmful to humans. Caution is needed only during installation, when a lot of volatile fibers are released.
- Durability. If the wooden house is properly insulated from the outside with mineral wool under the plaster, the finish will last the entire period of its operation.
- The ability to do the work with your own hands, since it does not represent a particular difficulty.
The disadvantage of quality Knauf products is only its high cost. Wetting and shrinkage occur in case of violation of installation technology, when vapor barrier and reinforcement are ignored.
Types of insulation
The trading network presents an extensive assortment of products designed for outdoor work on various surfaces. When making a choice, it is necessary to take into account the features and operational characteristics of each material. This will help to avoid mistakes and achieve the best result.
Glass wool
Glass wool is made from glass wastes and used containers. To increase operational characteristics, dolomite, technical soda and limestone are added to the main raw materials. Production is carried out by inflating a mass heated to a high temperature. The formation of long, thin threads that, when cooled, stick together.
The material is characterized by excellent insulating properties, resistance to decay and exposure to chemicals. The minus is that when squeezing the glass wool breaks and decreases in size, which reduces its insulation properties.
Slag
The basis of this type of mineral wool is blast furnace slag. Due to the properties of the raw materials, the fiber size is small, which negatively affects the stiffness of the mats, which is the lowest among analogues. However, affordable price and low thermal conductivity contribute to their high popularity. Mats quickly absorb moisture, but this drawback is offset by the installation of a vapor barrier. A feature of the material is the lack of elasticity, which leads to difficulties during its installation. Slots form that need to be filled with mounting foam. In addition, slabs are prone to shrinkage. To prevent it, the reinforcement method is used.
Stone
Basalt mineral wool facade for plastering is the best insulation material of this type in terms of performance. Products made from dolomite are characterized by high insulating properties, vapor permeability and elasticity. The material has an almost unlimited service life, as it is not subject to shrinkage. The cost of production is more affected by the cost of its production, since basalt is a by-product of the mining industry. The elasticity of the plates has a positive effect on the simplicity and speed of installation. The external insulator is taken by surprise into the openings prepared for it, there are no cracks after laying.
- Slag roll
- Glass wool
- Stone wool in slabs
The main stages of installation
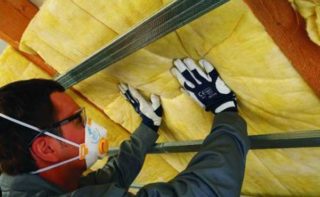
Insulation of the facade with mineral wool under the plaster is a simple process that does not require professional skills.
To work, you need the following set of tools and materials:
- roulette, level;
- a knife with a long blade, a hacksaw for metal;
- hammer drill;
- hammer, screwdriver, plaster spatulas, scissors, marker, stapler;
- paint brush or roller.
- steel profiles, corners;
- glue ceresit;
- membrane film;
- primer, antiseptic;
- mesh for reinforcement;
- facade plaster on mineral wool, acrylic paint;
- fixing hardware.
When working with mineral wool, a large number of small fibers are released. You need to work in overalls, a mask and rubber gloves. You should purchase a reliable and stable staircase or a set of scaffolding.
Foundation preparation
This event should be taken carefully and responsibly, as the walls will be closed without access and repair.
The preparatory phase is carried out in the following sequence:
- Removing all objects that protrude more than 2 cm. Cleaning the surface of dirt, dust, oil and grease stains.
- Examination of the base for rot and mold. Such areas should be scraped off to a clean layer.
- Surface treatment with antiseptic and a deep penetration primer. This will minimize the likelihood of developing fungus and mold.
- Fastening on the base of the starting profile. This part will serve as a supporting guide for the first row of plates, protect them from the penetration of insects and rodents.
- Drawing a marking. It is carried out under the dimensions of the plates so that they are fixed in a checkerboard pattern.
The end of the preparation of the walls is the installation of a vapor-permeable canvas on them. The fabric is nailed to wood and aerated concrete blocks with brackets, and glued to brick and concrete by quick-acting glue.
Fixing mineral wool
It is advisable to insulate the building with plates with the help of special through fixation anchors. This method will avoid the construction of an expensive crate, parts of which are cold bridges.
Fixation is carried out in the following sequence:
- Holes are drilled into the wall. The pins are inserted into them, on which the plates will be mounted. The anchors must be placed in the corners and in the middle of each rectangle at a distance of no more than 50 cm. In this case, you need to take a correction of 3-4 cm in order to install the insulation completely.
- Through-holes are made in heat insulators. To find them quickly, a black marker is used.
- The workpieces are mounted on the pins. Immediately after this, they are rigidly fixed with movable hats. To ensure a tight fit of the plates, you can use special glue, applying it pointwise, with a snake or in a spiral.
- The edges are closed and the last row is set.Fragments are cut so that they enter the openings with effort, without leaving cracks.
In conclusion, the insulation is sheathed with a membrane film. Its edges are connected to the material previously installed under the plates and sealed with tape.
Thermal insulation reinforcement
Reinforcement is intended to create a good adhesion of the plaster to the mineral wool, as well as to prevent its subsidence.
It is carried out in this order:
- At the top of the wall, dowels are installed, to which a grid or grille is suspended.
- The reinforcing cloth is fixed on the insulation with special glue.
- The edges of the mesh are tucked onto the starting profile, which gives the structure strength and tightness.
- Application to the reinforcement of a strong vapor-permeable composition.
Before starting the next stage, you need to wait for the glue to completely dry, and then treat it with a primer.
Plaster should be from the bottom up to prevent the solution from slipping. A plaster composition with a flow rate of up to 1000 g / m² should be used. A thick layer is not necessary, so as not to burden the structure. To reduce the working time and not to paint the facade after the mixture has hardened, it is possible to add pigment to it during kneading.