Cost, versatility and ease of installation are the main parameters when choosing building and finishing materials. PSB insulation is suitable for each of the requirements. It is important to know the characteristics and methods of work during the thermal insulation of houses and other buildings.
Terms and GOST
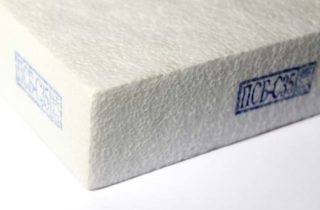
For all materials used in construction, legislation sets standards. Until 2014, GOST15588-86 was in force. Styrofoam sheets produced according to the parameters were assigned a symbol, for example, “PSB – S – 15–900x500x50 GOST 15588-86”.
Decoding means the following:
- P - plate;
- C - from suspension polystyrene;
- B - made without pressure;
- C - self-extinguishing, does not support combustion for more than 4 seconds upon termination of exposure to open flame;
- 15 - density grade;
- 900х500х50 - geometric dimensions.
To give incombustibility to the composition of the foam add flame retardants, which is indicated by the letter "C".
The density mark approximately corresponded to a mass of 1 m3 of foam. For civil engineering, products with a specific gravity of up to 15, 25 and 35 kg / m3 were produced.
The 1986 standard provided for an indication in the name of the maximum mass of material. On January 1, 2014, instead of an outdated document, the new GOST 15588-2014 began to operate.
Important changes were made to the consumer:
- plates received the name PPS (self-extinguishing polystyrene plates);
- specific gravity should now be no less than indicated in the name.
Some enterprises produce products according to the old GOST and call PSB boards, the new polystyrene has the name PPP.
An example of the current designation is PPS16F-R-B-1000h500h120 GOST 15588−2014.
- PPS is a polystyrene plate obtained by a pressureless method from a suspension.
- P - cut from large blocks.
- B - with a lateral edge selected in a quarter (A - with a rectangular edge).
- 1000x500x120 - geometric dimensions of the plate in mm.
The reasons why manufacturers produce some of the products according to the old standards:
- not all production equipment has been replaced;
- less stringent product requirements that satisfy private developers;
- material saving - for example, PSB-S-15 can have a mass of 12 to 15 kg / m3, and PPP-15 is only higher than this value.
The critical technical characteristics of the “old” and “new” boards are not significantly different.
Physicotechnical Properties
The popularity of the foam is directly affected by the technical characteristics:
- thermal conductivity
- density - measured in kg / m3 and indicated in the marking;
- geometric dimensions are reflected in the marking;
- water absorption;
- ultimate compressive strength.
The thermal conductivity of heat-insulating plates at a temperature of +10 degrees is in the range from 0.036 W / m * K for PSB-S-35 polystyrene to 0.041 for light products PSB-S-15. When the air warms up to 25 degrees, the indicators change slightly - by 1%.
The deviation of geometric dimensions by 2–5 mm is allowed. Tolerances do not affect the quality of insulation, since with such parameters the seams are small, they are easy to eliminate with mounting foam.
By water absorption is understood the increase in foam mass when it is in water for 24 hours.During this period, the foam absorbs from 2 (PSB – 35) to 4 (PSB – 15)% of the liquid of its mass. Thus, polystyrene boards are moisture resistant material.
The compressive strength will be determined by the scope of application of a particular brand of foam, for example, PSB-15 can not withstand loads, you can walk carefully on polystyrene foam 35.
The service life of the foam is limited only by the operating conditions - if the sheets are protected from adverse effects, 50 years is not the limit of use.
Benefits and Important Limitations of Use
The positive properties of the material are due to the composition and structure of the foam.
In construction are important:
- low weight;
- stability of shape and size under temperature fluctuations;
- ease of installation and manufacture of sheets of the right size;
- universality of use;
- long service life;
- resistance to decay and mold, not susceptible to colonization by parasites;
- lack of reaction to a slightly alkaline medium (cement);
- incombustibility;
- low thermal conductivity - 5 cm of polystyrene retain heat approximately the same as 70 cm of masonry or 30 cm of timber;
- environmental safety - in the composition of the finished plates, the styrene content is about 0.02%, which is released only after heating the foam above 80 ° C;
- windproof.
Disadvantages caused by:
- low stability when exposed to substances with an acid reaction;
- destruction by sunlight;
- exposure to rodent populations.
Polystyrene grades PSB and PPS should be used strictly for their intended purpose and technology, in this case, the durability of insulation is ensured.
Production technology
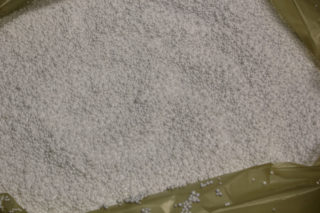
In the manufacturing process of plates using a minimum of components:
- polystyrene granules obtained during the refining process;
- pentane - natural gas condensate associated with the substance of the granules;
- flame retardants that make the material non-combustible;
- water vapor.
The production algorithm includes several stages:
- Foaming of raw materials - under the influence of water vapor and pressure, pentane expands in granules, increasing their volume by 20–70 times. The operation is stopped after the foam balls reach the required diameter.
- Hot air drying.
- Stabilization (bedding) for 4-24 hours. During this time, the balls cool completely, get their final size. The pentane remaining in the granules is replaced by air.
- Roasting under the influence of hot steam - balls are sintered into a single product with a volume of several cubic meters.
- Maturing (maturation) lasts from one day to 30 days. During this time, moisture evaporates completely, internal stresses in the product are stabilized.
- Cutting to size.
The waste after cutting is ground to individual balls and reused, introducing them at the stabilization stage.
In the final version, the manufacturer receives sheets of foamed propylene, consisting of 98% air and 2% polypropylene.
Violations of technology do not allow to obtain high quality material.
Equipment for the production of foam can be placed in small workshops. Small firms often produce low-quality products. Parameters are not checked by laboratory methods. It is impossible to focus on a low price when buying.
Ways to use
GOST provides for the use of foam sheets for thermal insulation:
- external walls of operated and newly constructed buildings and structures;
- individual rooms and industrial equipment, in the absence of contact between the plates and the volume of the internal premises;
- refrigerators at temperatures from –100 to + 80 ° C;
Foam is suitable for wet facade systems. It is used as a middle layer in panel constructions.
Appendix A to GOST indicates the scope of application of the foam grades depending on the density. PSB-S-15 or PPP grades from 10 to 15 are recommended for unloaded thermal insulation in three-layer structures made using the technology of a ventilated facade. PSB-S-25, PPS 16-20 are suitable for external walls for decoration with cement and composite plasters. Suitable material of this brand for insulation of floors under the screed, ceilings, roofs. PSB-S-35, or grade PPS 20 and higher, is used for the insulation layer under cement screed, for surfaces exposed to significant loads - paths, blind areas, foundations and socles of buildings for various purposes.
Ways to work with foam
Choosing a method and technology of insulation, take into account the requirements of GOST and common sense:
- Polyfoam should be protected from ultraviolet radiation - direct sunlight.
- Shock loads on the surface are excluded, it must be protected from physical impact.
- Sheets should not be open in the interior of the premises due to possible damage and fumes of styrene.
Foam insulation in private construction is carried out according to the technologies of a ventilated facade, a “wet” facade under the plaster, laying between layers of enclosing material.
Stucco finishing procedure
For work, choose PSB-S-25, or PPS-16F. It is impossible to use a foam with a lower density since it will not withstand the mass of cement. Buying expanded polystyrene plates with a specific gravity of 35 kg / m3 does not make sense - the material in all respects is not inferior to models 15 and 25, but it costs significantly more.
Warming algorithm:
- Walls made of bricks or expanded clay concrete (foam) blocks are cleaned of dust, dirt stains.
- The surface is leveled, knocking down the influx of masonry mortar. If necessary, plaster - it is important that there are no differences more than 1 cm per linear meter of the wall.
- A solution is prepared from a special cement-based polystyrene adhesive.
- Glue is applied to the plate with a layer of 0.5-1 cm, leveled with a notched trowel.
- PSB is glued to the wall, stacking the sheets in a checkerboard pattern. Another option is to use mounting adhesive-foam.
- For reliable fastening after 3-4 hours, polystyrene plates are additionally reinforced with dowels with wide caps at the rate of 5 dowels per m2. Close up the joints with mounting foam.
- The first layer of plaster is applied, for which they use the same glue that was used in paragraph 4. A plaster mesh is pressed into the plaster layer, the surface is leveled.
- After drying, the main plaster and puttying are carried out or decorative mixtures, for example, bark beetle, are used.
- Paint the surface.
Wet facade technology is rarely used for wooden houses. It is believed that the foam does not let air in and the house stops “breathing”, fungus and mold appear on the inner surface of the walls. The issue can be resolved by properly organized ventilation of the premises.
Insulation of hollow brick walls
The technology is simple. Between the internal load-bearing walls and the external finishing brick, cavities are left in which, as the masonry is erected, sheets of polystyrene are laid.
Use the cheapest PSB-15 foam option. The load in the wall cavity is completely absent, and the characteristics of the material are not inferior to a foam with a higher density.
When filling hollow walls, it is more profitable to use polystyrene foam crumb - it is cheaper and allows you to completely fill the internal space between the bricks. Material is sold in kraft bags with a volume of 1 m3.
Frame houses and polystyrene
A popular heater in the construction of frame houses is expanded polystyrene.
Polyfoam is mounted between the inner and outer skin. The gaps between the PSB and the bars are covered with mounting foam, this will eliminate the “cold bridges” and will not allow the wind to blow through the structure.
It is important to leave ventilation gaps between the polystyrene foam and the wall cladding so that moisture does not accumulate inside.
Ventilated facades
Houses decorated using the “ventilated facade” technology perfectly retain heat, prevent mold and mildew, and are attractive in appearance.
You can do the work on your own.
The method involves the creation of several layers. Warming procedure:
- Withstanding the level, the crate of wooden bars or galvanized profile is nailed to the wall. The bars are treated with an antiseptic with flame retardant additives. The cross section of the crate is equal to the thickness of the foam. The distance between the lags should be less than the size of the PSB by 0.5–1 cm so that the foam enters tightly.
- Mount polystyrene plates with dowels-fungi.
- The gaps are closed with foam.
- On the crate reinforce the waterproofing membrane, which will protect against external moisture.
- On top of the waterproofing, a 10-15 mm thick counter-lattice is nailed or screwed on.
- Mount the outer layer, which use various types of materials suitable for external use.
A counter-grill and a gap are needed so that moisture does not accumulate between the insulation and the outer layer, the space is freely blown (ventilated) with air.
Expanded polystyrene is a universal insulation suitable for use in any climatic zones. Work with the material is available to any user. Its use will increase comfort for residents and save money on payment of energy.