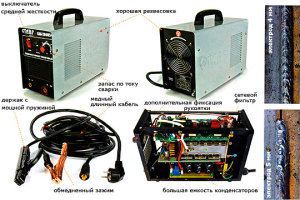
When designing a heating system, it is important to choose the right elements - a boiler, radiators and accessories. The configuration not always offered by manufacturers is suitable for operational parameters. And given the high cost, the question arises - how to weld the heating with your own hands: boilers, registers, combs? This can only be done if you have the appropriate device and minimal skills to work with it.
Choosing a welding machine and electrodes
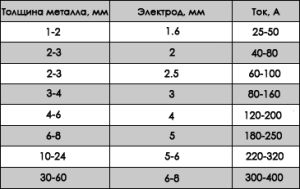
Currently, manufacturers offer several models of welding machines, with which you can make high-quality metal compounds of various grades. But before you properly weld the heating, you need to choose the optimal model. Consider the most popular types of devices and their main characteristics.
Transformer
The principle of operation is based on increasing the frequency of the incoming current. For this, step-up transformers are used. Despite the relatively large dimensions, this type of welding machine is best adapted to power grid surges. With it, you can properly weld a heating boiler in compliance with manufacturing technology.
Inverter
The formation of current according to the established parameters occurs due to the operation of electronic circuits. Characterized by a stable arc, which ultimately gives a high-quality seam. This must be taken into account before learning how to weld heating yourself. However, they are extremely sensitive to voltage drops in the network.
It is recommended to purchase a voltage stabilizer as additional equipment for inverter devices.
Is it possible to weld a boiler with my own hands for water heating using an inverter apparatus? Yes, but its characteristics must correspond to the parameters of the metal used. For the manufacture of heating elements, carbon steels are most often used.
Material table for heating welding
Product | steel grade | Type of electrodes |
Boiler body | St3, St3G and St4 | ANO3, MR-3, SSSI 13/45 |
Heat exchanger and boiler furnace | MCT2 and MCT3 | MTG-01K and MTG-02 |
Pipes with a diameter up to 100 mm | 12MX and 15XM | TSU-2XM |
Pipes with a diameter more than 100 mm | 12X2MFB |
You also need to know the dependence of the diameters of the electrodes on the thickness of the welded metal
As for the choice of a welding machine, experts recommend stopping on inverter models operating on alternating current. Their cost is slightly higher than that of transformers, but they are smaller and with their help you can make a high-quality weld. This is important to consider, since self-welding of a heating boiler must be of high quality.
The cost of the apparatus with a power of 7 kW, a welding current of up to 200 A and a maximum electrode diameter of 3.6 mm will be about 16 thousand rubles.
How to weld a heating boiler with your own hands
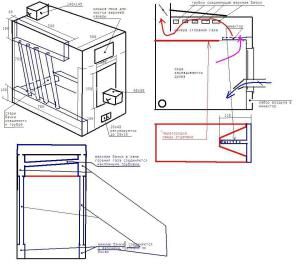
Before you weld the heating boiler yourself, you need to decide on its design. Preferably, it meets current safety and performance requirements. Therefore, as an example, a pyrolysis type boiler, made independently, will be considered.
How to weld a heating boiler of this type? In addition to the welding machine, the following materials and tools will be required for this:
- Sheet steel, grades of which are selected from the data of the table shown above.For the combustion chamber, the thickness of the metal should be 3-4 mm. The case can be made of steel of smaller thickness - 2-2.5 mm;
- Pipes for the manufacture of a heat exchanger. Their optimal diameter is 40 mm. This size will allow you to quickly heat up the coolant. The number of registers - from 3 to 6;
- How to weld a heating boiler without a cutting tool? It was best to use a “grinder” with special metal disks for cutting sheets;
- Doors for the combustion chamber and the blower. You also need to purchase cast iron grate. This must be done in advance, since the dimensions of the components will be used to make openings and fastening parts of the boiler;
- Level, tape measure and pencil (marker) for marking;
- Protective equipment - gloves, welder mask, transparent work glasses and clothing made of thick material with long sleeves.
For clarity, you can see how to weld heating in a private house. Video or photo materials will help in the work, since they clearly show all the stages and features of their implementation. However, this must be done only after drawing up the drawing and preparing all the tools and accessories. This applies to all stages of the manufacture of components, since it is impossible to weld the heating with your own hands, including boilers, registers, combs, without the correct scheme.
It is also important to prepare the place of work before welding the heating in the garage. Most often, the manufacturing process takes place in it. First you need to ensure maximum free space by removing excess objects.
For safety reasons, flammable liquids such as gasoline, oil, etc. should also be removed from the garage. And only after that you can begin to work - to weld the heating in the garage. Proper welding of the heating boiler consists in the manufacture of two components - directly the boiler body and the heat exchanger.
Heat exchanger
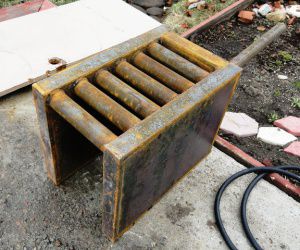
This element is made before the heating boiler is welded. Subsequently, it will be installed in a structure that will directly depend on its actual dimensions.
Structurally, it consists of 2 rectangular tanks interconnected by pipelines. The optimum thickness of the material should be 3-3.5 mm. This is due to high temperatures that will affect the surface. The specifics of its manufacture can be seen in the video - how to weld heating in a private house.
Housing
On steel sheets, the design is marked according to the drawings. First, the back panel is cut out and a partition is welded to it for the removal of wood (coal) gases. At this stage, you need to be very careful, since the weld can not always provide proper fastening. Then, the side and bottom are welded to the partition and the back wall.
It should be noted that it is quite problematic to weld a heating boiler itself. Therefore, this work is recommended to be performed by two. This is especially true for the installation phase of a finished heat exchanger. Its nozzles are placed in pre-prepared holes, and the pipes are spot-welded to the inside walls of the boiler.
Often there is a question - how to weld the heating inside the garage without forced ventilation. For this, work should only be carried out with the gates open to ensure a normal supply of fresh air.
The main problem with home-made designs is low work efficiency. To increase the efficiency, it is recommended to make double walls, between which a basalt refractory heat insulator is installed. You can weld such a boiler with your own hands for water heating, but for this you need to provide for an additional consumption of material. First, double walls are made, which are filled with insulation. Then, the further welding technology of the structure is fully consistent with the above.
How to weld a heating register with your own hands
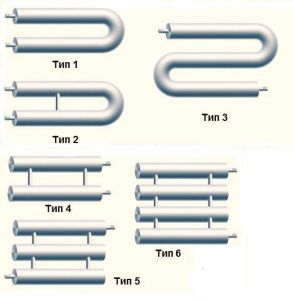
How to weld the heating register and in which cases it is recommended to install them? First you need to correctly understand their purpose. In fact, these are heating devices that should ensure maximum heat transfer from the hot water of the heating system to the room.
Before welding the heating registers, it is necessary to prepare the basic material for the manufacture of:
- Main pipes. They should be relatively large in diameter - up to 100 mm. For forced systems with high temperature conditions, it is recommended to use just such. It is better that the cross section of the pipe is round, since the profile structures will create a large hydraulic resistance, which is undesirable;
- In order to properly weld the heating register, pipes of smaller diameter will be needed, which will serve as pipes for the circulation of the coolant between the main horizontal ones. Their cross section should be in the range of 24-30 mm.
At the first stage of work, it is necessary to cut off all the pipes according to the previously prepared drawing. Then, before welding the heating registers, it is required to make plugs at the ends of large pipes. They are divided into two types - deaf and with inlet pipes. With the help of the latter, the coolant will move along the contour of the register.
The order of the work is as follows.
- In order to properly weld the register of the heating system, you must first cut all the pipes according to the drawing. For this, a “grinder” is used. At the end of the work, the end parts are cleaned;
- Making stubs. They need to use metal of the same thickness as that of pipes. The diameter of the plugs should be greater than the cross section of the pipe by the thickness of the metal. This is necessary to weld the mounting border. After their manufacture, welding is carried out;
- Before you weld the registers of the heating system using the adapter pipes, you must make holes in the pipes. This is best done with a welding machine, since it is impossible to cut a round hole with a grinder.
The final stage of work is the connection of large pipes into a single heating device - a register.
How to make a comb for DIY heating
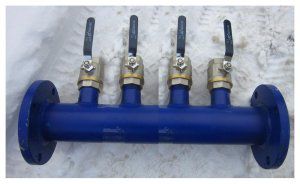
If you plan to install radiant heating, then it is necessary to make a collector for it. Is it possible and how to weld a comb for heating so that it functions normally? Yes, but first you need to find out its purpose.
It is necessary for the distribution of coolant in the individual circuits of the system. Outwardly, this is the pipe in which the pipes must be installed. They are connected to individual heating mains.
Since welding the comb for heating is similar to the manufacturing process of the register, there is no need to focus on this stage. It is important to note the difference in the connecting elements located at the ends of the structure. It can be flanges (as in the photo), or adapter couplings from the smaller diameter of the heating pipes (32 or 40) to the larger combs (50 mm is the optimal size).
For the manufacture of elements of the heating system, before you start to properly weld the heating, you need to carefully study the possible design options. It must be remembered that the larger the size of the combustion chamber, the more powerful the installation. Therefore, you must first calculate its volume.
For example, you can watch a video of welding heating in a private house, namely, the manufacture of a pyrolysis boiler: