If it is necessary to equip a warm floor on a wooden floor, there are fears regarding the unreliability of the wooden base, which needs preparation and additional strengthening. Dispelling them will help the description of heating systems, the installation of which is permissible under certain conditions.
Choosing the type of floor heating
Before arranging a warm floor, you will need to familiarize yourself with existing varieties of heating structures. According to their device and method of obtaining heating energy, they are divided into the following types:
- electric heating systems;
- water heated floors (TP).
The first of these varieties work on the principle of converting electrical energy into heat, and special equipment is used to equip them. Water heating floors are a complex structure of steel or copper pipes with a heat carrier circulating through them. Due to the low thermal conductivity of wood in this case, preference is given to electric models having a large thermal yield.
They, in turn, are classified as follows:
- electrical systems called “heating cable”;
- film or infrared underfloor heating;
- constructions mounted on the basis of heating mats.
Each of the listed varieties has its own advantages and disadvantages, the choice of a suitable one for a particular situation is determined by the preferences of the user himself.
Features of choice
When comparing options for electric floors, the following important points should be noted:
- A typical cable is supplied in the form of bays of a certain length, differing in their thermal output. The value of the power developed by such a design is on average 120-180 W / sq. Meter.
- Electric mats as separate elements of a warm floor are made by laying cable cores on a solid foundation with a certain step and have the same heat transfer.
- Infrared floors are arranged on the basis of IR films with electric contacts located along their edges (the power developed by them is 150–220 W / sq. Meter).
Compared to common water floors, electrical analogues are easier to install and take up less space in the apartment. When laying them, it is not always necessary to dismantle the rough floor base. They heat up much faster and allow you to set the desired temperature if desired.
Electrical structures have long operating periods (up to 50 years) and rarely fail. At the same time, when they are mounted on a wood base, there is always a risk of short-circuit and the resulting fire with the possibility of fire. Another drawback of such floors is the high current consumption, which forces the owners of the house or apartment to update the existing wiring.
Also, the choice of heating system depends on what kind of finish coating it is supposed to lay on top of the structure. If ceramic tile is chosen for these purposes, preference is given to mats or a typical heat cable. Under a parquet board or a more plastic and vulnerable laminate it is more advisable to use an infrared system.
General procedure for installing TP on a wooden floor
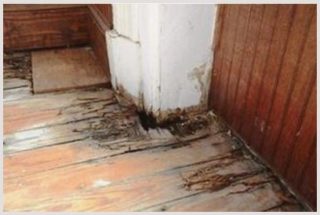
The generally accepted procedure for installing a heating system on wooden floors is reduced to the following mandatory procedures:
- Dismantling of old plank coating.
- Replacing rotten floorboards with new samples.
- Reassembling the base while warming it in any convenient way (using stone wool slabs, for example).
- Installation of heating elements (mats, cable or IR film).
- Connection to an electric network.
- Test inclusion and verification of the heating system.
- Choosing the right material and finishing coating.
- Testing the entire system for performance.
Possible nuances of the upcoming work depend on the type of underfloor heating chosen and the technology of laying it on a prepared foundation. Each of them has its advantages and disadvantages, which should be considered in advance.
Options and pipe laying technique
There are several known technologies for equipping TP in rooms with floor coverings based on conventional boards. For the average user, the simplest options are suitable, associated with mounting on lags and laying on special guides (rack method).
Lagging option
Flooring begins with the preparation of a solid wood base. If rotten floorboards are found in the existing coating, they are replaced with fresh boards. Further actions are carried out in the following sequence:
- At the edges of the repaired floor, two side beams with grooves for transverse support-floors are attached to the brackets.
- At first, ready-made lags are laid in them, set strictly according to the level and fixed in any convenient way.
- After their fixation, plates of the selected insulation are placed between the individual transverse boards. Most often, these are plates based on foam or basalt wool.
- In the pre-prepared grooves, the heating elements themselves (electrical cables, for example) are placed, fixed by means of jumpers applied to the kit.
Upon completion of laying the heat-insulating mat, they begin to design a protective flooring, which can be used as sheets of moisture-proof plywood with a thickness of at least 3 cm. A finishing floor from linoleum or typeset parquet is installed on top of the finished base.
On rails
This method is more suitable for water heated floors. For the implementation of rack technology, additional details will be required, as which special guides are used. In this case, the installation procedure looks like this:
- A reliable base is prepared from laid floorboards, damaged or decayed samples of which are replaced by new ones.
- It is carefully leveled, supporting bars are mounted on top, free niches are covered with mineral wool mats or foam plates.
- A layer of waterproofing is laid on top of them, covered from above with moisture-proof plywood.
- Ready-made rack guides are taken, which are packed directly on its surface according to a pre-compiled scheme for laying a “snake” from pipes. The TP elements will be fixed in them.
- The resulting gaps are sealed with reflective material.
Separate tubes of a water heat-insulated floor are placed in the prepared grooves, which are closed from above by heat-reflecting material. This type of installation of the heating system is quite laborious, but it guarantees the reliability of its operation and does not require significant costs from the contractor.
Specialist advice
Specialists in laying warm water floors on a wooden floor are advised to adhere to the following recommendations:
- On turning areas, the sharp angles of the guide rails are pre-rounded, which eliminates the possibility of damage to the tubes with a coolant.
- The aluminum foil used to retain heat is selected with a thickness of at least 50 microns.
- During installation, it is pressed into the grooves with effort, enveloping each recess in them.
- Foil sheets can be prevented from shifting by fixing them on rails using a construction stapler.
- For better heat transfer, the water pipes are also wrapped with aluminum foil before laying.
At the end of the main work, the mounted water floor is independently connected to the heating system. At the same time, it is compulsory crimped, eliminating the possibility of leaks. If during visual inspection no leakage is detected, proceed to the next stage of work associated with the installation of the finish coating.
Advantages of underfloor heating on a wooden floor
Installation of TP on the surface of already laid boards with preliminary insulation of the base has a number of advantages, manifested:
- The work is carried out according to absolutely “dry” technologies, the implementation of which dispenses with the tedious procedures of mixing and pouring concrete mixtures.
- To prepare the base, it is enough to align the existing coating and lay the bars on it under the logs.
- Thermal insulation procedures are simplified, since ready-made niches are already available for laying mats or plates of a heat insulator.
- The floor itself is mounted much easier, since there is no need for special fixators of thermal elements. They are installed and fixed directly on the lags.
The design of the final coating (linoleum, for example) is facilitated, so it can be mounted on plywood flooring, fixed on the same rails or lags.