Wood walls are distinguished by their ability to retain heat for a long time. But despite this, they also need additional insulation, since the tree shrinks during operation. An external insulation layer protects the house not only from the cold, but also from mechanical influences, fungi, rodents and insects. To create high-quality thermal insulation, you should first understand the varieties of heaters and their features. There are many types of materials, as well as manufacturers (foam, foam and others). Each has its positive and negative traits.
Features of warming wooden houses
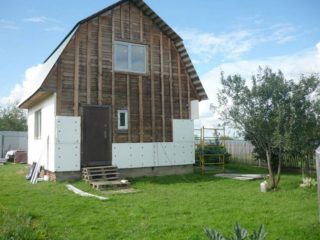
Wood absorbs liquid. To reduce this property, it is treated with special water-repellent agents. If the house has normal ventilation, water will not have a negative effect. If air exchange is disturbed, condensation will accumulate, which leads to swelling of the tree and the appearance of fungi and mold.
During installation, several requirements must be observed:
- Do not insulate damp walls;
- must have vapor permeability;
- thermal insulation must be sheathed with a membrane on both sides;
- it is necessary to leave a distance between the insulation and the final finish.
If the walls of the house will be painted, you should buy paint and sealant with a good level of vapor permeability. The surface before work must be cleaned of dirt, moss, hooks, bugs and other pests.
Types of insulation for wood
The range of insulation is quite wide, but not all materials are vapor permeable. Insulating materials based on mineral wool, ecowool or cellulose are suitable for wood. Choosing the right insulation depends on many factors.
Stone wool
It is made of rocks, in particular basalt. In addition to stone fibers, the composition of the material includes binders and hydrophobized additives. The material is non-combustible and can withstand temperatures up to 600 ° C, which is especially important for wooden buildings. It has low thermal conductivity, has a high level of vapor permeability. Release form - plates, mats coated with foil, kraft paper or fiberglass.
Installation of basalt plates does not cause difficulties, so it can be done independently without the help of specialists. They keep their shape well during operation and do not shrink when laying according to all requirements. The weight of the plates is small.
Among the disadvantages, we can distinguish fragility of the fibers and high cost. You can only work with such products using personal protective equipment and in a respirator, as small particles can get into the respiratory tract.
Slag wool
External insulation is made from blast furnace slag - metallurgical waste. Due to this, the cost of insulation is low, and the maximum temperature is 300 ° C. Release form - rolls and plates. Usually a foil coating is made. Rigidity is low, so the material can be used to warm curved surfaces. It retains heat well, absorbs sound. Prevents the development of mold. Rodents and insects also do not like this material. The service life is about 50 years.
Slag is poorly tolerated by temperature jumps, when wet, it releases acid, which corrodes the metal.The fibers are sharp, so when laying it is necessary to use protective equipment so that the material does not get on the skin and does not cause irritation.
Glass wool
The material is durable, resilient, and has a high degree of sound insulation. It is made from glass melts, in which limestone, borax, dolomite and other components are added. Polymers, sometimes bitumen, act as a binding component. Elasticity is achieved through long fibers.
Glass wool has a good indicator of vapor permeability and holds heat well from the inside. It is not adversely affected by aggressive chemicals. It is characterized by incombustibility and the ability to maintain heating up to 450 ° C. Release form - plates, rolls, mats coated with foil and fiberglass.
The main disadvantage is fragility and barb. Be sure to work in protection for the hands, eyes and respiratory tract. Protection should be strong and reliable, as ordinary clothes will not save from glass wool. The respirator will allow you not to breathe dust particles that are formed during installation.
Ecowool
Cellulose insulation or ecowool is a material that is made from the waste of the paper and cardboard industry. To improve performance, manufacturers add antiseptics and flame retardants to the fibers. Ecowool absorbs moisture and gives it away without changing the characteristics. Prevents condensation. Absorbs sounds and vibration. Does not emit harmful substances. Insects and rodents do not start in ecowool.
The main disadvantage is the styling technology. To work with ecowool you need skills and abilities, so you need to call a specialist.
The process of thermal insulation with mineral wool boards
Any home craftsman can make an independent warming of the walls of a wooden summer cottage with mineral wool. For work, you need a quality reliable tool and supplies:
- a pencil to create markup;
- level;
- ruler, tape measure;
- jigsaw;
- fasteners (screws and dowels);
- antiseptic for walls;
- membrane for hydro and vapor barrier;
- construction stapler;
- acrylic based sealant.
Next, you need to calculate the volume of materials. For this, the wall area is calculated, from which the area of the openings is subtracted, and divided by the area of one plate. The resulting value will be the minimum required number of plates. It is better to buy them with a margin so that in case of damage you can replace it with a suitable one. When stacking in two layers, the value should be multiplied by 2.
Training
Before starting work, prepare a wooden surface. To do this, it is freed from defects and treated with an antiseptic. Installation can only begin after complete drying.
Warming can only be done in warm weather, so that the walls are not damp or frozen. It is necessary to carefully examine the interventional seams and, if there are voids, seal them with sealant. Similarly, get rid of old cracks in the tree.
The primer should be applied with a brush, practicing all the bumps and indentations. It can be applied in two layers if the wood quickly absorbs the composition. It is necessary to wait for the complete drying of the logs, after which you can insulate the private home.
Insulation Installation
Step-by-step instructions for wall insulation:
- Mounting a vapor barrier. The membrane is laid in horizontal stripes from the bottom of the walls. Fixing is done on the stapler.
- Installation of extreme bars on a level at a distance of 5-10 cm from the corners. Fixation on self-tapping screws. The remaining parts are fixed so that the distance between them is 10 mm less than the width of the insulation material.
- Slabs of mineral wool are placed in the cells of the crate without gaps. They are fixed with dowels. The second layer is laid so that the joints between the plates on the first layer are overlapped.
- Mounting the protective membrane. It is installed on the brackets. It is necessary to ensure that the material fits snugly to the base.
- Stacking racks kontroreshetki. They provide clearance for ventilation.
You can also use the frameless method of warming a log house outside. With this installation, the guides are attached to the walls on metal U-shaped suspensions. In the plates you need to make holes for suspensions. Additionally, the design is fixed with dowels. A membrane is placed on top.
After all the work, you can finish the facade. You can install facade siding and other finishing materials on thermal insulation.
Ecowool laying
To lay the material on the walls, you must first make markings for the crate. Guides from a bar are laid vertically at a distance of 50-60 cm from each other. After that, you need to make the casing of moisture-resistant plates at a distance of 80-100 cm from the ground. The lower part is sewn up with boards. Ecowool is unpacked and placed in a container. Beat it at a low speed with a mixer so that there are no lumps left.
The insulation pours out between the walls and the plasterboard with filling all the corners. After the next row of casing is attached. Then, priming and finishing is done.
The most difficult thing is the distribution of ecowool in the upper part of the crate, so the work must be done carefully and accurately, trying to better compact the material.