Polyethylene pipes for the gas pipeline are rapidly replacing steel counterparts that have been used in residential buildings and office buildings for decades. PE pipes are no less popular for arranging a gas pipeline in private construction. Using inexpensive, lightweight and practical material allows you to save on purchases and significantly reduce the time of laying communications. To make the decision that was optimal in all respects was easier, you should familiarize yourself with the assortment of polyethylene pipes for gas pipelines, study their technical characteristics, advantages and disadvantages, and installation and use features.
Varieties of polyethylene pipes for a gas pipeline
Polyethylene pipes for the gas pipeline are manufactured using continuous extrusion technology in accordance with the requirements of GOST R 50838-2009. A soft, preheated polymer mass is pushed through the slot, cools down, after which the finished product is painted and marked on it. This production method allows you to get pipes of almost any length, which reduces the time of construction of the pipeline, and a reduced number of joints increases its reliability.
The industry produces gas pipes from polyethylene of the following grades:
- PE-80. They have a wall thickness of 2-3 mm, are designed for a maximum pressure of 6 MPa, and are used for laying household communications.
- PE-100. Wall thickness 3.5 mm, designed for pressures up to 12 MPa. They are distinguished by higher strength and density, serve for laying local and main gas pipelines.
By its structure, a gas polyethylene pipe may have such a device:
- standard - only polyethylene, without additives and additives;
- reinforced - with additional layers located outside or inside to improve operational characteristics;
- with a protective transport cover, which is removed before installation.
The size of one link varies between 5-25 m. Provided that the product will not be cut after the extruder, the length of one fragment can be 200-700 m, depending on its cross section.
The diameter of the products corresponds to the standards accepted in the construction industry and amounts to 20-630 mm. For the construction of trunk facilities, a polyethylene pipe for gas with a cross section of 1200 mm is used.
The color of the products indicates their composition, purpose and scope. Different types of products are painted in black, yellow, orange and blue.
The product is marked, which gives a decoding of such indicators:
- material;
- section;
- appointment;
- manufacturer;
- batch number;
- date of manufacture.
Marking is applied by embossing, paint or in a combined way.
Pipe specifications
There are a number of criteria by which plastic pipes are selected. Product indicators are taken into account when designing underground structures, taking into account the conditions of their operation and the characteristics of the transported substances.
The selection of material is carried out according to the following characteristics:
- SDR An indicator indicating the ratio of the diameter of the pipe to the thickness of its wall. The lower the SDR, the higher the pressure that it can withstand.
- Mrs. The number indicates the maximum permissible pressure at which the utilization of communications is allowed.It is measured in pascals (MPa) and is 3-10 MPa depending on the brand of products.
- Bending radius. It is measured in external diameters and averages 25. The thinner the pipe, the more material can be twisted into one bay. And this is an important factor for the storage, transportation and installation of products.
The temperature range of operation of polymer communications is ± 40ºС, which makes polyethylene an ideal material for underground installation.
Scope of polyethylene pipes for the gas pipeline
Due to its many advantages, polyethylene gas pipelines have gained high popularity in many areas of activity.
The material can be used for the construction of such structures:
- Main gas pipelines of federal significance. Pipes of large diameter are able to pass a large amount of blue fuel per unit time. The only condition is the deepening of the route below the freezing point of the soil.
- Internal wiring inside the house and apartments. Characteristics of polyethylene products comply with the requirements for structures of this type.
- Ducts in the ventilation system. Used material grade PE-80, characterized by sufficient strength. Pipes are used for passing complex curved sections outside the walls and in their internal voids.
- Water pipes. Polyethylene does not emit harmful substances and is chemically inert. On communications, you can pump technical and drinking water.
- Technological pipelines. They are used in the pharmaceutical and food industries to transport liquids of various classes, including toxic ones.
- Sheath for laying telecommunication and electric cables. Inside such a sheath, the wires are protected against pressure during movement of the soil, insects, rodents, dampness, aggressive effects of alkaline soil.
The scope of use of polyethylene pipes is not limited to use for construction purposes. They are successfully used as an element of decor and interior design. Products are used for the manufacture of garden arches, frame for greenhouses and pools.
Mounting Features
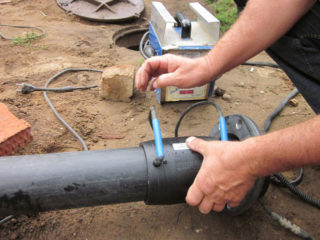
Only licensed organizations with special equipment and qualified personnel are allowed to lay gas supply systems. Subsequent repairs and maintenance of communications can only be carried out by these companies.
The following requirements are imposed on the compounds:
- tightness;
- strength;
- uniformity;
- reliability;
- durability;
- resistance to aggressive chemicals.
The installation of PE pipes on gas is carried out by a team equipped with earthmoving equipment and equipment for connecting pipes. Installation is carried out in accordance with the project, which takes into account the data of soil studies and previously laid underground utilities. During the work, various connection methods can be used.
The butt method is often used when laying large-diameter highways. For its implementation, welding equipment is used.
The process takes place in the following sequence:
- Preparation of material and tools.
- Installation of equipment, its programming.
- Cleaning pipe ends from dirt, cleaning joints.
- Laying fragments in holders, checking their alignment.
- Welding performance.
- Cooling material.
- Seam marking.
- Moving welding equipment.
The connection is carried out by setting the polymer with the subsequent docking. The process of diffusion occurs, after cooling, both links become a single whole.
The electrofusion method is used when laying small diameter channels, making corners and branches.It uses the same melting technology, but it is carried out not at the ends, but outside. A heating coil is installed on the inner walls of the coupling, which, when the current is connected, melts the plastic, which leads to the creation of a monolithic connection.
Docking is carried out in the following order:
- Preparation of material and tools.
- Cleaning pipe ends from dirt, cleaning joints.
- Laying fragments on supports, checking their alignment.
- Coupling installation, pipe connection.
- The inclusion of electricity, fusion of fragments.
- Cooling material.
- Seam marking.
- Moving welding equipment.
The choice of voltage and heating time is made for each type and model of material. Electrofusion couplings are characterized by increased strength, reliability and durability.
The detachable method is used extremely rarely, mainly to create temporary communications or systems with the prospect of their further modernization. The abutting elements are inserted into the housing, which is tightened on both sides by crimp rings. Such a connection is characterized by sufficient strength, but fragility. To keep it tight, it is necessary to tighten the nuts periodically. Another option is welding / gluing to the ends of the flanges, followed by screwing the parts with bolts. The advantage of this solution is that the docking parts can be removed and reused.
The main advantages and disadvantages of polyethylene pipes for the gas pipeline
Like any building materials, gas pipeline polyethylene pipes have their advantages and disadvantages. Each of them is important in deciding on the construction of a gas supply system.
Material Advantages:
- There is no need to provide grounding, as PE is an excellent insulator.
- Sufficient durability. The highway is capable of withstanding soil pressure without damage and deformation.
- No corrosion. Plastic is not susceptible to moisture, the effects of salts and alkalis contained in the soil.
- Simplicity and speed of installation. The pipes are light, a small number of joints are made when assembling the trunk.
- Flexibility and elasticity. When the ground moves communications do not break and do not break.
- Durability. Manufacturers give a guarantee on their products within 40-80 years.
Polyethylene also has disadvantages. The main thing is the limited range of operating temperature. The material is permeable to oxygen, which limits its use in open areas and indoors.