Log structures remain in demand, although many new building materials have appeared. The tree retains heat perfectly, it regulates the level of humidity in the room well. However, sometimes in winter, residents of such houses observe the freezing of individual walls. Therefore, you should understand how to insulate a log house from a log.
Requirements for the properties of insulation materials
Choosing a heater for a log house, it is necessary to take into account the characteristics of wood. Suitable material should have the following properties:
- the same vapor permeability as wood;
- moisture resistance, which will protect the tree from moisture accumulation, decay;
- fire safety;
- immunity to the occurrence of fungus, pests;
- allow air to pass through, create natural ventilation;
- have a structure that allows the insulation to fit snugly against the wooden walls.
Warming a house from a log outside or inside will significantly reduce heat loss and heating costs. Living at home will be much more comfortable.
For the purpose of warming a wooden house you can not use:
- Styrofoam;
- polystyrene foam;
- foam for installation;
- sealants.
The use of vapor-proof materials leads to the fact that the tree begins to rot. If you protect it from the inside with a film, the wooden house will turn into a thermos, the meaning of building such a house will be lost.
Recommended materials for warming a log house
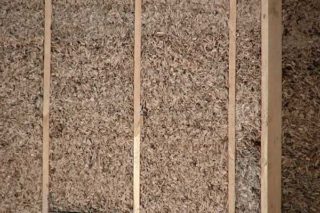
For wood, only natural insulation should be used: sawdust, seaweed, straw and others. With external insulation of an old wooden house, ecowool and mineral wool can be used. The latter are inexpensive, easy to install, in technological properties similar to natural materials for thermal insulation.
Sawdust
In terms of heat preservation, they are no different from modern thermal insulation.
Advantages:
- low price;
- environmental friendliness.
Disadvantages:
- quickly ignite;
- rot in case of moisture;
- pests often settle in them.
In pure form, such material is not used. Typically, insulation of a log from a log outside is carried out by granules or pressed boards. The first fall asleep from the bottom and to the top. Since such a material gives some shrinkage, over time it will require backfilling. Pressed plates are securely attached to the crate.
Ecowool
The insulation is made from cellulose fibers (80%) and antiseptics (20%). The latter protects it from mold and rodents. The material is suitable for warming any room.
With proper use, ecowool easily takes the necessary shape, fits well to logs. For this reason, it retains heat for a long time.
Advantages:
- reliability;
- resistance to burning;
- inaccessible to rodents;
- prevents the appearance of mold, fungi;
- low thermal conductivity;
- environmental friendliness.
Disadvantages:
- applied using special equipment;
- shrinks;
- under the influence of high temperatures begins to smolder.
Ecowool is applied to a pre-installed crate by spraying. The surface should be moistened with water. After spraying, a layer forms, which subsequently protects the structure from freezing.
Straw
Straw has a thermal conductivity 4 times less than that of wood, and 8 times less than that of brick.
Advantages:
- the ability to absorb moisture, if necessary, to give it to the air (while harmful impurities are removed from the latter);
- provides oxygen circulation in the room, ventilation even with closed windows and doors;
- low price;
- ecological cleanliness;
- excellent soundproofing properties (due to the porous structure).
Disadvantages:
- duration of work when using;
- high labor costs.
Despite the fragility of the insulation, it contains 3 times more silica than wood. As a building material, straw is stronger and more durable than wood.
Seaweed
The insulating material of the chamber is made from algae emissions after a storm. It has become widespread due to availability.
Advantages:
- excellent thermal insulation properties;
- good noise isolator;
- rodents and insects do not start in the material due to the high content of calcium salts;
- does not decay;
- does not support combustion.
The main disadvantage: it easily breaks as a result of mechanical stress.
The chamber is able to absorb moisture in case of excess in the room and give out if the air is too dry.
Due to the high content of nutrients (including iodine), cam creates a suitable microclimate for people suffering from disorders of the central nervous system and respiratory system.
Mineral wool
It is made from rock alloys (silicate), but has a synthetic base. Mineral wool is available in the form of mats, plates, which provides easy attachment to the surfaces of the log house.
Advantages:
- significant resistance to decay;
- good thermal insulation characteristics;
- fire safety.
Disadvantages:
- deforms with time;
- under the influence of high temperature emits harmful substances;
- amenable to mold.
Mineral wool at the base can have various substances: molten glass, blast furnace slag, basalt rock.
The process of internal insulation of a wooden structure
Before warming a log house outside with your own hands, you should consider the option of thermal insulation of the structure from the inside. It is possible that these measures will be enough, and you will not have to spoil the external walls.
Ceiling
Since heat exits through the ceiling to a greater extent, it is worth starting the insulation of the house from it. For this purpose, you need to prepare:
- knife;
- hammer;
- glue for a tile;
- hacksaw;
- screwdriver.
Materials:
- insulation;
- nails, screws;
- edged boards;
- foam for installation;
- drywall.
The process consists of the following steps:
- Prepare the frame from the boards. Please note that it will affect the future height of the ceiling. Edged boards are fixed at a distance of no more than a meter.
- For the purpose of waterproofing, carefully fill the space between the installed boards with a glassine.
- Lay mineral wool. If necessary, glue may be used.
- Sheathe drywall, screwing it to the frame.
In conclusion, it remains to do the decoration and cladding.
Walls
During the insulation of walls in the room, you need to take into account that condensation will appear on their surfaces due to the temperature difference: the outside of the structure is very cold, the inside is much warmer. The problem can be solved with the help of a vapor barrier film used together with a heater.
To work, you need to purchase the following tools, materials:
- roulette wheel;
- a screwdriver;
- plumb line;
- level;
- a chisel;
- drill (percussion);
- hammer;
- dowels, screws;
- screwdriver;
- installation foam, felt;
- wooden bars;
- insulation (ecowool, mineral wool), drywall, putty.
Wall insulation technology:
- Close up cracks with foam, felt.
- Build the crate with wooden beams. They are attached to the wall with screws, dowels after 30 cm. The approximate distance between adjacent boards is 1 m. Attach the same horizontal ones over the vertical boards.
- To prevent the appearance of fungus, treat wooden elements with an antiseptic.
- Between the fixed bars, lay the insulation tightly without glue.
- Make vapor barrier using a plastic film (lay on the insulation).
At the end of the work, you should complete the decoration: sheathe the walls with drywall (fasten to the crate), carefully glue all the cracks.
Floor
To complete the work, you will need:
- hammer;
- drill;
- electric jigsaw;
- hacksaw;
- knife, pencil, nails;
- plane;
- roulette, level;
- insulation.
The main stages of work on floor insulation:
- Level the surface, eliminate defects.
- Lay a waterproofing material to protect the insulation from moisture.
- Put logs at a distance of not more than 50 cm. Suitable lag size is 5 × 10 cm, thickness - at least 5 cm.
- Between the last put mineral wool.
- Place a PVC membrane on top.
The floor will be completely ready after laying the flooring from waterproof plywood or chipboard.
Windows and doors
Filling gaps and holes in frames is very easy.
Tools and materials:
- aluminum ruler;
- polyurethane foam.
Using an aluminum ruler, you need to check the tightness of doors and windows, poking it in accessible places near the frames. Found cracks to blow out foam. It is recommended to use soft mounting foam.