Warm floors are becoming more popular than traditional heating systems, as it is easier to arrange, often more economical. You can mount the system yourself. However, laying a warm floor in a screed, depending on its type, is carried out according to strict technology.
Types of underfloor heating
Before starting installation, you need to determine the type of heating system. It can be electric or water. The choice depends on the area of the house, the availability of a standard heating design, the preferences of the owner.
Electric
The electric option provides for laying a cable in the cable tie, which heats up when connected to the network. It is effective, but it can not be used everywhere. Another option for this design - mats with electric cable. The infrared warm floor in the form of carbon rods or a film deserves special attention.
Each type of electrical system is reliable, durable, and requires a dry foundation during installation. When arranging, do not forget about insulation and grounding. A temperature controller is used to control the heating temperature. Tile these systems in apartments.
Water
Water floor heating is suitable for a private house. Such a system becomes an alternative to standard designs, as it is able to warm the floor and the entire room. This option is a little more expensive to install, but its cost pays off in the first years of operation. Heating occurs due to the circulation of hot coolant through the pipes.
Properties of underfloor heating
Heating with underfloor heating has a certain advantage over the classical system. Heated air rises from the floor, cools down above, which creates a good microclimate. The following design advantages can be distinguished:
- energy saving;
- all parts of the system are hidden under the floor, so they do not spoil the interior of the rooms;
- there is no need to install radiators, between which ribs dust is collected;
- organization of the optimal level of humidity.
The arrangement of the construction of the warm floor involves the installation of several layers: rough screed, waterproofing, parts of the system. After this, the concrete mixture is poured and the final finish is laid.
Necessary tools and materials for work
Before laying the system, you need to select the appropriate tools and materials. The master will need a film for waterproofing, a thermal insulator, a damping tape, concrete mix and a special composition for leveling the base. Depending on the type of system, the following tools are needed:
- Water heating. Need a gas burner, a cutter for pipes made of metal, pipe cutter. Reinforcing tape, a collector, a mixing unit are used for laying elements.
- Infrared film. Requires a hammer drill, adjustable spanners, building level, contact clamps, electrical tape, pliers. You also need a thermal reflector, which is placed under the film, a temperature sensor, a regulator, electrical wiring, construction tape to glue the joints of waterproofing.
- Cable. Need a thick wire, couplings for connection, tile adhesive, corrugated tube for cable insulation.
Some manufacturers of underfloor heating systems produce complete with the necessary tool.It is important to choose high-quality products, because otherwise you will have to open the entire floor to repair the structure.
Stage-by-stage installation of electric underfloor heating
To lay the electric underfloor heating under the screed, you must strictly comply with the installation technology. First, a rough screed is laid, after which the base is prepared to equip the heating system.
Rough screed
It is the lowest layer and is intended to eliminate differences in the height of the base. If the floor will be laid on a flat floor slab, a rough screed is not necessary. For its filling, special self-leveling mixtures are used. Their advantage is the absence of the need to install marking beacons.
Thermal insulation
The base is pre-cleaned of dust, debris and dirt with a construction vacuum cleaner. For thermal insulation, a cork substrate, polypropylene, is used. To increase the effectiveness of underfloor heating will allow foil film. To fix the sheets together, glue, construction tape or dowels are used. The thickness of the foil layer is not less than 300 microns. At the same stage, the reinforcing mesh is laid.
Heating cable
The electric cable is laid out in the form of a snake, parallel to the wall. To fix it, a mounting tape is used if a reinforcing mesh was not used. It is laid on the base in increments of 50 cm. Self-tapping screws are used for fastening. The cable is pulled along the mounting tape and fixed on special brackets.
The cable connects to a temperature sensor hidden in a corrugated tube. It is located near the end of the system and displayed up. When pouring, the screed must be observed so that concrete does not get into the tube. Lastly, a thermostat is connected.
Concrete screed
Before laying the mixture, you need to check the performance of the warm floor. Filling is carried out after the installation of beacons at positive temperature. The solution is laid out at a time on the entire floor area. The mixture is poured from the far corner towards the door.
A technological gap is established between the wall and the screed with the help of a damping tape, which will prevent the concrete from cracking during expansion.
Installation of underfloor heating underfloor heating
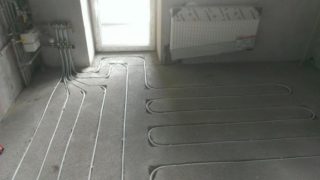
Laying a warm water floor in the screed should begin after preliminary preparation of the project. The heat transfer of the system, the length of the pipes, as well as the installation step are calculated. At the same stage, finishing is selected.
Training
First you need to determine the location of the distribution cabinet, bring main pipelines to it. If an automatic control system is installed, strobes in the walls are cut for wiring. If the base is soil, it must be removed and pour the rough screed. The surface should be clean and even (the difference in height should not exceed 5 mm per 1 m).
Waterproofing
If moisture gets on the system, its effectiveness will decrease, so the process of installing waterproofing is mandatory. For this, a thick plastic film is used. At the junction of the floor and wall, a damper tape is laid, the thickness of which is 0.6-1.2 cm.
Pipe laying
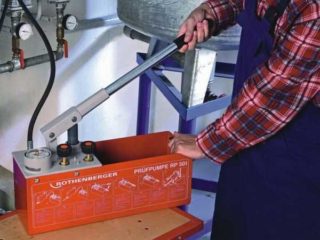
Installation of pipes is carried out after laying the heat insulator - expanded polystyrene. Pipes are mounted on the foam itself, with anchor brackets or on a reinforcing mesh. The most common mounting scheme is a snail. The maximum length of the circuit is 80 m. Connect the pipes to the collector carefully, without confusing anything. At this stage, water is launched into the system and its operability is checked.If the heating is uniform, you can fill.
Pouring screed
The screed under the warm floor is poured with a cement-sand mixture. The minimum thickness of the screed is 3 cm from the upper edge of the pipes, the optimum pressure of which is 6 bar. Do not dry the layer with heaters. It will be possible to start the system after the screed gains strength - after 28 days.
Fair floor
As a finishing finish, tiles, laminate or other materials are used. Their selection is carried out at the stage of designing the project.
The warm floor will make the microclimate in the room comfortable and help warm the room, saving money on heating. Installation and configuration of equipment can be done independently.