For an autonomous heating main of a private house or bath, a stationary stove is used. Due to the high heat transfer and efficiency, a comfortable temperature is quickly pumped. To reduce the cost of arranging the system, a boiler in a heating furnace can be made independently.
The need for boiler equipment in a heating furnace
When fuel is burned in a furnace, useful heat is directed into the air or leaks through a chimney. In some cases, a low-power heating unit is not enough for efficient heating of the coolant. Furnace boilers are justified for several reasons:
- full heating of distant rooms - no need to connect additional electrical appliances;
- the creation of a thermal curtain - the windows do not sweat, the house does not undergo decay processes;
- improvement of circulation inside the heating system - the temperature difference is preserved in different sections of the coolant;
- Corrosion elimination on metal parts of the furnace.
You can combine stove heating with radiator wiring in the house using the boiler built into the heating or cooking surface.
DIY heat exchanger manufacturing
It is allowed to integrate flat, air and tubular heat exchangers with one's own hand. When constructing the device, it is necessary to take into account the labor costs and the cost of the project.
Simple fixture
A flat heat exchanger increases the efficiency of the stove; it is installed vertically or horizontally in the boiler. It is easy to remove soot and soot from the element, and due to its large volume it can be adapted to the needs of hot water supply.
The plate heat exchanger looks like a pipe of large diameter, inside of which there is a smaller one. Water moves along it in the heated state, the cooling process takes place in a large nozzle.
Do-it-yourself construction is made of copper tubes. One should be larger than the other by 4 mm in diameter. The work is carried out as follows:
- Fastening by welding a side tee on two sides of the tube from the outside.
- Installing a smaller nozzle.
- Welding an element to the ends of a large tube in a pre-fixed position.
- Installation of short tubes at the outlet to the tees. They are needed for the movement of the coolant.
- Connection of parts by segments with alternate welding of tees to the side parts in the form of a snake.
Steel tubes should be larger than copper, assembly is carried out block by block.
Complex recuperator
The heat-exchange boiler for furnace heating looks like a tank with pipes and a heater. It consists of two sectors with mutual heating. The coolant circulates, getting into the closed loop of the tank, heats up to 180 degrees. Water is routed to the main line after passing through small pipes.
To weld the heat exchanger yourself, you will need such materials:
- finished tank with a capacity of 90 to 110 l;
- sheet steel 2.5-3 mm thick, if the tank is made by hand;
- anode;
- 2 copper pipes up to 4 m long for heating elements;
- device that controls the heating power.
Before starting work, it is necessary to make a drawing of the finished product, and then proceed to assembly:
- Install the tank at a height of 1 m from the floor and 3 m from the stove.
- Make two holes on the right side of the stove and on the top left.
- Draw a tap for water heating devices from below, tilting it by 2-3 degrees.
- Connect the upper branch in the opposite direction with an inclination of 20 degrees.
- Insert 2 drain taps into the bottom outlet for the tank and for the system.
- Seal the holes tightly to evenly warm the rooms.
- Bend the copper tube in a spiral shape.
- Install the finished coil in the tank, bring the ends out and fix them.
- Attach threaded fittings to the coil end.
- Connect a ready-made power regulator to the pipe.
- Throw terminals on the thermostat for power, and then wires.
- Install an anode to prevent tank wear from temperature fluctuations.
- Seal the seams and all parts with a special tool.
The finished heat exchanger is filled with water and checked for leaks. If everything is in order, the boiler for the stove can be put into operation.
Creating a heating wiring diagram
Combining the furnace with a water boiler and connecting the circuit to the heating system can be done in two ways.
Open system
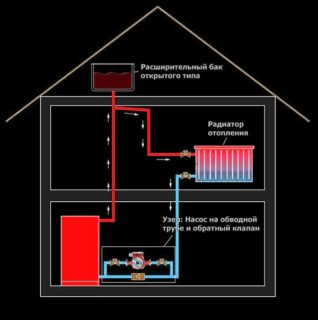
The coolant moves in a gravitational manner, so the installation of a circulation pump is required. It is put on bypass, reduces the temperature difference between the return and supply, increases the speed of water and the quality of heat transfer. Without electricity, the line will work on the principle of gravity.
To organize it, you will need to increase the line and the horizontal slopes in diameter. The open system is equipped with a 32 mm distributing collector with an inclination from 3 to 5 mm per linear meter. The expansion tank is located at the top, it receives air from the communications.
Closed system
The radiator network provides for the forced movement of water. Traction in this case creates a pump. It also pumps up pressure from 1 Bar for a cold coolant. The membrane type tank is located below. A shut-off valve is used to connect it to the highway. Safety devices (air vent, pressure gauge, bleed valve) are required.
An autonomous boiler in a brick oven is best connected by gravity.
Expert opinion on a home-made heat exchanger in a heating furnace
Professionals make several comments about installing the boiler in a heating installation:
- The effectiveness of the result of a combined system without overpayments.
- The ability to use any type of fuel. Sawdust, coal, pallets and firewood stored in a dry place are suitable.
- The furnace unit, which has a water boiler, does not need to be constantly heated. Fuel is laid once every 12-24 hours.
- The system, where a long type of combustion is implemented, allows you to warm up the building with high quality and provide hot water.
- In the absence of welding skills and an understanding of the manufacturing process, homemade heating appliances should be avoided. As an exception, installation in a country house or in settlements with power outages is considered.
- The optimal type of chimney for a stove with a boiler tank is bell-type. The heat exchanger in the form of a register of pipes with a large cross-section is placed inside.
- In order not to splurge on copper fittings, you can work with seamless pipes. They do not crack when heated.
A home-made solid fuel unit with a water circuit can be used in winter. It quickly and efficiently heats large housing, ensures uninterrupted supply of hot water. Before starting work, you need to choose a quality material for the heat exchanger, which will not be heated from the surface of the furnace structure.