Reliability and productivity of heating will increase the collector group for a warm floor. This unit will simplify operation and installation. At any time, you can repair it without compromising functionality. The device is a mechanism distributing coolant flows between the boiler or the main line and the underfloor heating.
The main types of collectors
The operation scheme of the device is as follows - water from the boiler enters the storage tank. Such a tank is placed at a height above the "comb". The coolant enters the distributor with shut-off and control valves. From the distributor flows diverge on separate branches. The outlet pipes are assembled at the bottom of the “comb” to be sent for heating to the boiler.
Typically, the unit is a piece of pipe with a certain number of bends. As the technical task becomes more complicated, the complexity increases dozens of times, the complexity of the automation settings, and installation are complicated at times.
Stainless steel
Stainless steel manifolds are stronger than brass. They have a large flow area, equalizing the pressure of the flows of different consumers of the coolant. The Valtek collector for heating is designed for an average of 50 years of operation at a pressure of 10 atm. and temperature up to 130 degrees.
Branded models are reliable - even the appearance of a weld does not lead to corrosion. Buying models of cheap manufacturers, you can run into low-quality metal and surface corrosion.
Made of polypropylene
Polymer comb is made of polypropylene pipes. This lightweight material is not as durable as steel, but it will last more than one year with success. Plastic collectors are exceptionally cheap. The use is justified during the circulation of the coolant in several heating devices. If the main task is to save, this option is suitable.
The stores feature models with fittings and manifolds with shut-off valves.
Combined fittings are used to transition to a threaded metal product.
Plastic combs are common in Ukraine. To strengthen the structure, up to 30% fiberglass is added to PA66 polyamide in factory technopolymers to increase strength.
The disadvantage of polymer products is thick walls. They narrow the section of the passage with the same dimensions of the part. Steel nodes are stronger, walls can be made thinner - the internal section increases and allows several percent more fluid to pass per unit of time under the same conditions.
Another disadvantage of polymers is oxygen permeability. Fiberglass reinforcement minimizes it. But oxygen diffusion is present.
The advantages of polymer products are resistance to aggressive environments, electrochemical corrosion, low thermal conductivity. With the same tube length, the polymer loses less heat than steel or brass.
Made of brass
This material leads in the manufacture of combs. For production in Europe, a hollow brass rod is made. For decades, products have been made from it - cut to the desired length, drilled holes for flow meters, valves, cut threads. Present on the market and stamped models.
Due to rising prices for brass, manufacturers switched to cheap materials - steel and plastic. However, brass models are still preferable. They have one drawback - washing out zinc.But it is leveled by chromium plating or nickel plating.
In low-temperature conditions, the advantages of small expansion of brass are leveled and are relative.
Design features
Due to their characteristic appearance, heating system installers call the collector “comb”. This is a complex site. He is able to redirect incoming coolant flows to different floors heating circuits. Advanced devices dehydrate the coolant, regulate its temperature, flow rate.
The collector acts as an intermediary between the boiler and the consumer. Consists of 2 nodes:
- supply comb for delivery of coolant;
- return comb for returning the cooled coolant to the boiler or main pipe.
A pair of combs makes up the collector group; they distribute heat to a large number of circuits and heating devices. At the exits of the comb, exhaust valves of the shut-off or control type are placed. They block the coolant or change the supply volume to the circuits. Closing one of the channels allows you to repair without disconnecting other consumers.
Additional devices are mounted on the comb housing to increase the efficiency of the heating system:
- flow meters;
- venting and draining valves;
- heat meters.
If it is not possible to achieve equal heating circuits, they include a circulation pump that equalizes the volume of fluid passage.
With a different number of circuits
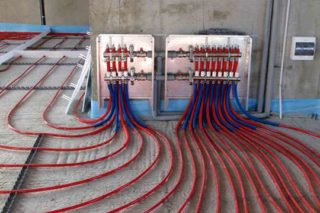
The need for a collector appears when there are two or more heating circuits. This is convenient for beam distributing pipes to create a system of underfloor heating - individually for each heating device.
The heating system has been stacked for decades. It is deepened into the floor screed and is not removable. Therefore, the collector group has the ability to block several channels at once. Each circuit in a similar system is disabled for repair, maintenance, emergency work.
Previously, collectors were mounted from a variety of tees together with shutoff valves. Now technology allows you to make the product according to customer needs. The finished collector group consists of two combs with a bore diameter of 1 inch. This diameter is used in most cases. The outputs for heating appliances are 0.5 inches; if necessary, combine with small diameters equipped with adapters of ¾ inch.
Prefabricated collector groups enter the market with the number of connection points - from 2 to 12.
Collector groups are the central element of the water floor heating system. The main module of the collectors themselves are mixing group nodes.
In individual house-building, the units are connected to a high-temperature heating system. A coolant with such a temperature cannot heat the floor, otherwise the deformation of the materials will begin, harmful substances will be released from the flooring, and you can’t walk barefoot. Lower the temperature by introducing mixing groups. When cold water is added from the return line, the coolant reaches the values prescribed by SNiP - 26 degrees for rooms with a constant presence of people, 31 degrees - with a temporary stay, 35 degrees - along the axis of the bathroom heating line.
Mixing groups are necessary when distributing flows to high-temperature boilers going to heating radiators and for floor heating.
Pump assembly options
The group mixing unit consists of a control valve and a circulation pump designed for forced circulation of the working medium in heating systems. The more collector groups assembled, the more powerful the pump is.
The Grundfos UPS Series pump operates 24 hours a day in all types of heating systems. The speed of the pump is regulated stepwise. In addition to the underfloor heating, up to 3 radiators of batteries can be connected, so power adjustment is very useful. A similar mechanism works from a household outlet with a voltage of 220 V, economical, no noise. These characteristics are important for use in heating private homes.
With flow meter
Mandatory attribute of the heating system are flow meters. They are necessary for regulating the flow of coolant due to the different lengths of the pipes. Without them, the resistance in short pipes is less than in long pipes. This will unbalance the water system. The flow meter creates a uniform circulation of the working medium in all system circuits.
It is possible to operate a system of heated floors without a flow meter. But to achieve fine temperature control will not work - the inertia of the warm floor is large. You have to wait for cooling to adjust the shut-off valve. With manual adjustment, you will have to remember the position of the valve. The flow meter is marked.
Sometimes collector kits for underfloor heating with a flowmeter cost less than a separate collector with inlet taps.
Valve Selection Criteria
If the circulation pump regulates the flow rate of the working fluid, the control valve limits the temperature of the fluid. An autonomous boiler produces a coolant with a temperature of 95 degrees. In the heating system, the water is not much colder - 80-90 degrees. The normal temperature of the liquid in the heated floors is 35-55 degrees. The control thermostat determines the temperature of the fluid flow and instructs the valve to open the opening from the return stroke. Fueled by cool water, the temperature drops. Upon reaching a temperature of 55 degrees in the pipes, the circulation pump is disconnected from the network by a thermostat, after which the volume of the passing coolant decreases.
The three-way valve is a unit with 1 output and 2 inputs. The valve shutter is opened by a temperature sensor located in the valve.
When choosing a valve, the following indicators are taken into account:
- The volume of the room for heating. Small rooms do not require complex nodes with automation. Balconies, toilets, corridors easily work under the supervision of simple appliances. Heating large areas requires an automatic valve with a built-in diaphragm opening temperature sensor.
- The volume of fluid passed through. This indicator is determined when writing a draft heating system. The valve must meet the requirements for fluid passage. Otherwise, it will fail.
- Section diameter for connection to heating pipes. At different indicators, adapters are used.
- The material of manufacture. Quality valves are made of bronze or brass - materials with a small coefficient of expansion. They do not change properties when in contact with a hot coolant.
The three-way valve is a complex part. It is necessary to choose reliable models of well-known manufacturers. Warranty, specifications, certificate, test report are checked upon purchase.
Before installation, the valve must be checked - the minimum temperature value of the control ring is set and the flow of hot water is passed. A serviceable valve must shut off this flow.
Heating homes with two or more floors involves the use of several water circuits of varying lengths. A combination of a three-way valve and a servo drive with a controller allows you to apply hot coolant to a certain room or send it for heating.
Initially, a servo for heating is not included. But the presence of a servomotor allows you to adjust the temperature depending on the time of day.
For a valve with an electric motor, the triggers are electromagnets or low-power servomotors.
DIY collector group
Finding the right finished product is not always possible. Sometimes it’s easier to save money and make a collector yourself from a popular material - polypropylene.
In the calculations of the product, the golden rule must be observed - the sum of the outgoing flows is equal to or slightly less than the incoming. Failure to comply with this principle threatens uneven distribution of the coolant.
The advantages of a home-made system:
- taking into account heating features without unnecessary collector elements;
- saving money.
The propylene collector includes 2 parts:
- The first part takes the coolant from the main pipeline, distributes the heat to consumers. In this element, it is important to make the contours independent, overlapping in case of prevention. To do this, just close one of the taps.
- The second part regulates the pressure in each individual circuit. Due to this, the intensity of the coolant circulation changes. The efficiency of heat consumers depends on the correct setting of this option.
The right project will simplify the creation of an effective collector for specific customer conditions. For correct assembly, a number of heating system parameters are evaluated:
- number of heating circuits;
- quantity and characteristics of the final equipment - temperature, pressure, power;
- the likelihood of placing additional heating elements;
- number of add-ons - sensors, pumps, taps.
After that, consider ways to connect the circuits to the collector:
- supply of coolant from above or below from electric or gas boilers;
- in the presence of a circulation pump, the connection is made from the end of the collector;
- indirect heating boilers and solid fuel boilers cut only from the end;
- heating circuits are supplied from the top or bottom.
The project should be printed on paper and visualized. Strict adherence to sizes and proportions will help to avoid installation errors.
The distance between the manifold nozzles is about 20 cm. Smaller - complicates maintenance. Larger - increases the size. The assembly technology of the comb is divided into stages:
- procurement of materials based on the materials of the design assignment;
- pipe connection according to the statement of work;
- connecting pipes using the right tools;
- thorough cleaning and sealing of joints and seams;
- leak test by damping the nozzles and supplying water under pressure;
- installation on a regular place after hardening of sealant and paint.
The comb is easily created with your own hands. It is important to take the project design seriously, to observe the parameters of the pipes and assembly. A self-assembled collector will take into account the individual parameters of the system.