To maintain operability, flushing and pressure testing of the heating system should take place regularly. This is done by specially trained people. The process itself is regulated by regulatory documents. To prevent the detection of leaks, the pipes are pressurized with a pressure exceeding the working pressure in the heating system.
What is flushing and pressure testing of the heating system
Works for the preparation and resumption of uninterrupted functioning of the heating guarantee trouble-free flow of the coolant.
Flushing
If the batteries in your apartment become worse than before, there are several reasons:
- poor boiler performance;
- pump breakdown;
- pipe airing.
During many years of operation, pipes, heaters, and collectors accumulate debris, scale particles, and rust. Growing inside, they clog the passage hole for the coolant, the porous structure reduces the heat capacity of the metal parts of the heating devices.
The consequences of blockages:
- burn-out of the heat exchanger requiring its replacement;
- temperature difference in batteries;
- noise in the pump with subsequent failure;
- boiler breakdown.
To eliminate, prevent pollution, flushing is performed.
The decrease in heating efficiency occurs for 2 main reasons:
- The appearance of mineral deposits. Un galvanized pipes willingly take to the surface salt of calcium, magnesium. With galvanized pipes, such problems do not arise.
- The growth of sludge in pipe sections with a low velocity of the coolant. Multisection cast-iron radiators are subject to this phenomenon. The dependence is proportional to the increase in the volume and number of sections.
People flush simple appliances and heating pipes in private homes on their own. This is easy to do with knowledge and equipment. Heating systems and batteries in apartment buildings are best left to the professionals responsible for their work and giving a guarantee.
There are 2 ways to clean the system:
- special hydropneumatic equipment;
- chemical reagents.
The basis of chemicals is acid.
Crimping
This procedure is designed to check the hydraulic system for weak points. Tests are carried out using excess pressure of the water circuit or pneumatic method.
Equipment for work
Cordless washing of engineering heating systems with chemical reagents is carried out by an eliminator apparatus with manual or automatic reverse. There are imported and Russian samples on the market, differing in pumping volume, type of reverse and other functions. The work is carried out with a washing reagent. Then stop the action of washing with a neutralizing solution. Electrical devices create overpressure and drive off the chemical solution.
For hydropneumatic cleaning, you need a pneumatic pump that can catch up to 6 atm. and higher.
The hand pump is a cuvette with a plunger pump located on the side and a drive handle. Shut-off valves cut off the water after heating, others - to drain the coolant from the device. The plunger pump raises the pressure to 60 bar. The disadvantage when used in private homes is hours of work at high cost of muscular energy.
Professional washers use automatic appliances.They set the pressure limit, upon reaching which the automation switches off the unit. Professional models maintain a pressure of 40-100 bar. Industrial pressure stations produce up to 1000 atmospheres.
Pressure Testing Stages
The work is carried out with the following frequency:
- when starting a new system;
- annually after the heating season;
- after flushing or repairing the heating main with the replacement of pipes.
For apartment buildings, the preparation is as follows:
- Inspection of valves in elevators, central pipes, risers. On cast-iron valves, the seals are changed, the paronite gaskets between the flanges of the joints are renewed, the unsuitable bolted joints are changed.
- By the method of visual observation, pipes and fittings are examined for the presence of cracks, chips, corrosion, defects. Make repairs if necessary.
- Check the thermal insulation of risers, main pipes in the basements.
Pressure testing procedures and testing are carried out taking into account the parameters of heaters, indoor heating equipment. The standards allow the use of operating pressures up to 6 bar for cast-iron radiators. When they are in the walls, a maximum of 10 bar.
Hydraulic tests are carried out as follows: the system is checked as a whole, then a pressure higher than the working pressure is applied to the thermal unit.
According to Regulation 115, clause 9.2.13., Tests shall be carried out with a pressure not lower than
- 1 MPa - elevators, heaters for heating and domestic hot water;
- 0.6 MPa - cast iron and steel heating radiators;
- 1MPa - convector, panel heaters;
- working pressure plus 0.5-1 MPa for hot water supply;
- pressure recorded in the manufacturer's instructions for air heaters.
The test pressure in steam systems is selected by the manufacturer from maximum to operating minimum:
- minimum - not less than 0.2 MPa, but not less than 1.25 working;
- the maximum is established by calculation of strength according to the standards;
Crimping takes place at a temperature of + 5 degrees. If negative - in emergency cases.
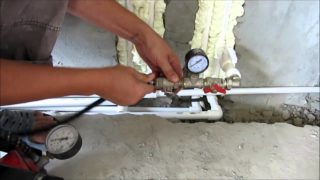
Stages of crimping:
- Filling the system with cold water. When working, the temperature of the liquid is not more than 45 degrees. The pressure rises gradually. Monitoring is carried out using a manometer.
- Upon reaching the set pressure, the system remains at rest for about 30 minutes.
- During downtime, an inspection is made for leaks in pipes, batteries. Make sure there are no smudges. The control method is placement in hazardous places of toilet paper or wrapping pipes around it. With leaks, spots of water, silt are visible.
- Monitoring takes place according to the readings of the pressure gauge. Leak occurs in a place inaccessible to observation. A drop in pressure will warn of this.
At the end of the crimping, an act of serviceability is issued.
Tests are conducted by certified companies. In apartment buildings, it is forbidden to conduct heating work independently. This is done by employees of operating organizations - ZhEK, UK, ZhEU, REU. They are required to undergo annual certification at MOEK.
Flushing heating systems
The accumulation of sludge, scale in pipes and radiators reduce the quality of heating - only 1 mm of scale reduces the heat transfer of the device by 15%. To normalize the temperature in the house will have to increase the heat transfer of the boiler, and this is an additional cost for fuel and labor. Scale is inherently a heat insulator. Its thermal conductivity is 40 times lower than the metal composition. Therefore, even a thin layer leads to a decrease in heat return by the heat carrier. The scale is aggressive. It interacts with the metal and leads to increased corrosion. Aggressive scale for several years creates fistulas, corrodes welds.
In an apartment building
Utilities are constantly using the hydropneumatic flushing method of the heating system. Subject to technology, this is an effective way.
The principle of operation is simple - first the water is discharged, then it is fed back to the heating system by pumps. Under the influence of the heat carrier flow, the scale flakes off and comes out with water when draining.
Step by step sequence:
- All cranes are shut off before operation.
- The end faces of heating batteries are unscrewed using a special key.
- The return valve closes.
- The air pump is connected to the valve located after the valve.
- The return is reset.
- Pressure is pumped into pneumatics over 6 atm.
- A valve opens to which pneumatic equipment is connected.
- In turn, the risers overlap. At the same time up to 10 pieces - this will make the washing procedure effective.
The next step is to switch the system to drop in the opposite direction:
- The discharge closes, the valve connected to the apparatus closes, the pneumatics are turned off.
- The open valve slides, after which a similar one opens on the return.
- Water is discharged - the air pump is connected through the valve in the opposite direction, the valve opens, pneumatics is turned on. The fluid will flow in the reverse direction.
The cleaning productivity is determined visually - if a clean liquid starts to come out, washing can be completed. Dirt is poured into cooked dishes. If possible, a hose is connected and the dirty coolant is discharged into the sewer.
In a private house
Washing in a private house is difficult to do with your own hands, but really, after reading the instructions. It is made in two ways:
- Flow method. Cleaning from toxins and deposits by this method consists in the complete filling of all devices with the coolant with the air vent valve left open. After filling, the valve closes. Simultaneously with the supply of compressed air, a drain hole opens. The air-water mixture continues to be supplied until clean water appears. The amount of flushing fluid is 3-5 times the working value. Therefore, pre-prepare drain tanks or drain into the sewer.
- Flushing with filling. The system is filled with valves closed. Air is supplied under pressure for a period of 5-10 minutes. in the inlet pipe, the outlet is closed. After the supply of compressed air is completed, the flushing is drained together with dirt and scale.
The volume of fluid and air supplied is calculated individually. Incorrect calculation will lead to numerous pipe ruptures, and not to flushing.
In private homes, collectors, shutoff valves, boilers, boilers, joints of connections with appliances, circulation pumps, and heated floors are checked.
It is not necessary to buy washing equipment - it is leased. If it is necessary to draw up official papers and a test report, a special team is called up. The estimated cost of services is 1000-2600 rubles / hour.
Flushing and crimping requirements
Pressure testing is carried out exclusively at a positive air temperature - above +5 degrees. If negative, it is allowed during the liquidation of accidents. Tests are successful in such cases:
- there is no fogging of welds, leaks in heating devices - boilers, pipes, radiators, faucets and other equipment;
- pressure reduction by pressure gauge does not exceed 0.2 bar in 5 min;
- in panel heating, a decrease in the pressure gauge does not exceed 0.1 bar per quarter hour;
- in hot water supply, the coolant pressure drop below 0.5 bar in 10 min;
- for plastic pipes, the pressure drop in the system is below 0.6 bar in 30 minutes, in the next 2 hours - less than 0.2 bar;
- when tested with air pressure, a pressure drop of up to 0.1 bar is allowed in 5 minutes.
Flushing and pressure testing of the heating system are regulated by special papers.
P. 9.2.12.strength and density tests, according to the "Rules of Technical Operation" (PTE), of thermal power plants from the Ministry of Energy of Russia. Types of tests are regulated - primary, periodic, extraordinary. According to the paragraph of the "Rules", flushing systems is carried out with the start of commissioning. Also annually at the end of the heating period, after accidents, pipe changes or major repairs.
The estimated volume of the coolant must exceed the worker by 3-5 times and at the exit be completely bright. Rinse with technical or tap water.
The commissioning of an unverified heating system is prohibited.
Rinsing improves coolant circulation and heat transfer, cost savings, comfortable living.
Rule 115, clause 9.2.13. "Strength tests." In the requirements of tenders, OKPD code 2 of category 43.22.12.120 for flushing and crimping the heating system is assigned to:
- installation of heating equipment;
- installation and maintenance of central heating control systems;
- connection to district heating systems;
- installation and maintenance of domestic boilers and boilers;
- installation of ventilation, refrigeration equipment in residential and non-residential premises.
Does not include: repair and maintenance of industrial boilers, air conditioners, refrigerators, installation of solar collectors, baseboard heaters, chimney cleaning.
The test results are recorded in the act of testing the strength and density. If the results are unsatisfactory, flaws are eliminated and the tests are carried out again.